The Fetal Medicine Research Institute
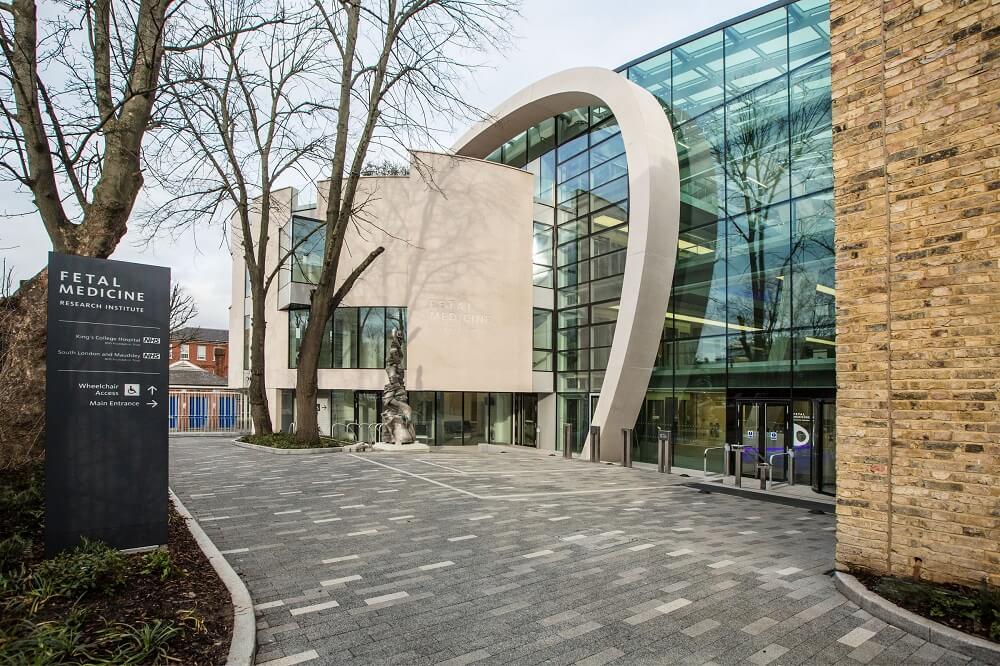
Paul Feely & Associates acted as the Principal Designer on a major new concrete batching plant project in Huddersfield for long standing client Myers ReadyMix.
This was a multi-million-pound investment in a cutting edge facility designed to serve high volume commercial, civil, and industrial construction projects across Yorkshire.
With the capability to produce up to 120m³ of concrete per hour, the new Huddersfield plant provides a significant increase in regional supply capacity. Designed and built in partnership with Liebherr, a global leader in concrete batching systems, the facility prioritises efficiency, reliability, and long term operational safety.
About the Client: Myers ReadyMix
Myers ReadyMix, part of the wider Myers Group,
is one of Yorkshire’s most established suppliers of high-quality ready-mixed concrete. Operating batching plants in Huddersfield, Brighouse, and Skipton, the company has been serving the region for over 60 years and is known for its commitment to quality, service, and innovation.
Their new Huddersfield site was developed to:
-
Provide a continuous and accredited concrete supply to major projects across West Yorkshire and far beyond.
-
Minimise operational downtime by using Liebherr’s proven batching systems
-
Deliver faster and more consistent concrete mixes, helping clients meet demanding project timelines
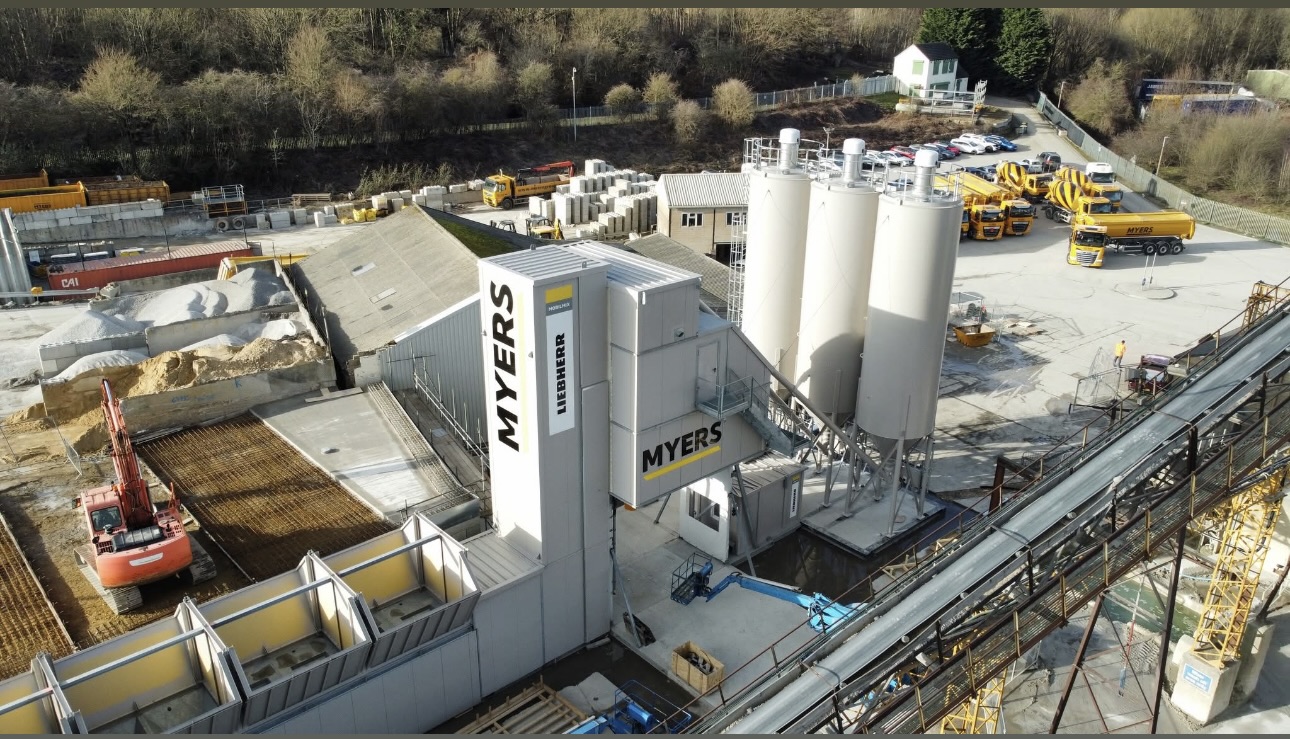
Our Role: Health & Safety Built Into the Design
The key to the success of this project was simple: early engagement.
Myers involved us right from the pre-construction stage because of our track record delivering complex, high-risk concrete industry projects. That early input meant we could help shape the plant’s layout, design features, and construction programme with safety embedded at every stage.
As Principal Designer, we coordinated closely with all project stakeholders, including:
- The Myers project team, to ensure the client’s operational needs were reflected in the safety design
- The Principal Contractor, to manage pre-construction phase planning and safety documentation
- A range of specialist subcontractors and engineers, to coordinate temporary works and technical sequences
- The Liebherr engineering team, to ensure the integration of complex machinery and plant equipment was done safely and compliantly
Project Complexity: Managing Risk Through Design
This was a high-risk, multi-disciplinary build with several layers of complexity:
- The project involved installation of high risk machinery with moving parts, requiring detailed consideration of guarding, isolation, and future maintenance.
- Complex lifting operations and heavy cranage were required during installation, demanding safe sequencing and coordination across trades.
- We were responsible for overseeing temporary works planning, ensuring structures and foundations could be safely installed with minimal disruption to the site.
- The project required precise multi-trade coordination under strict programme deadlines, which meant effective communication and daily monitoring of risk.
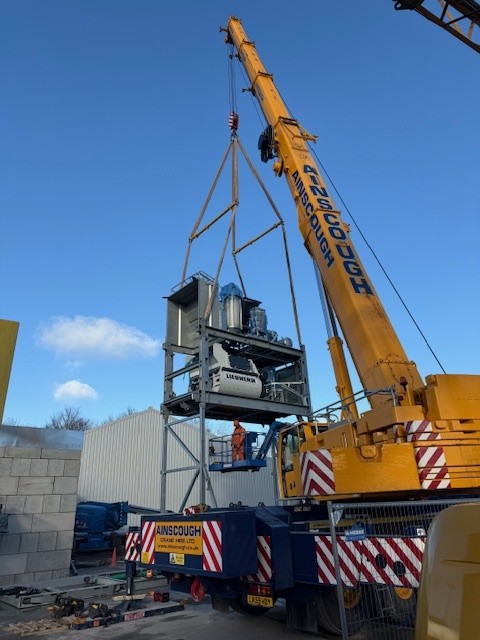
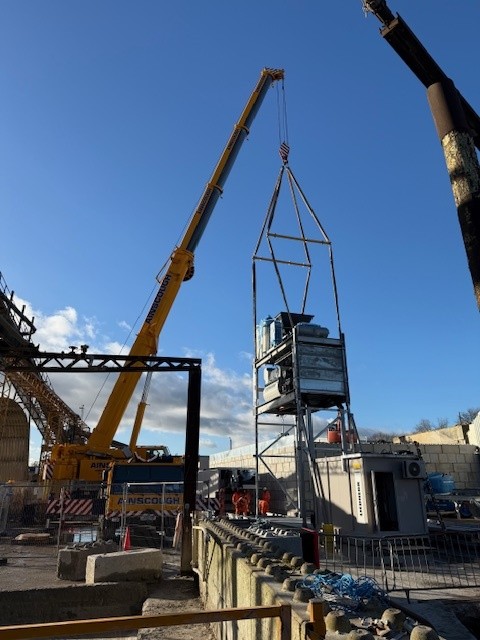
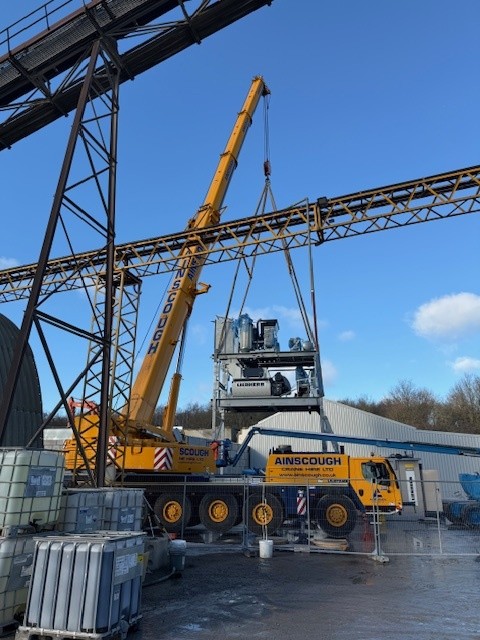
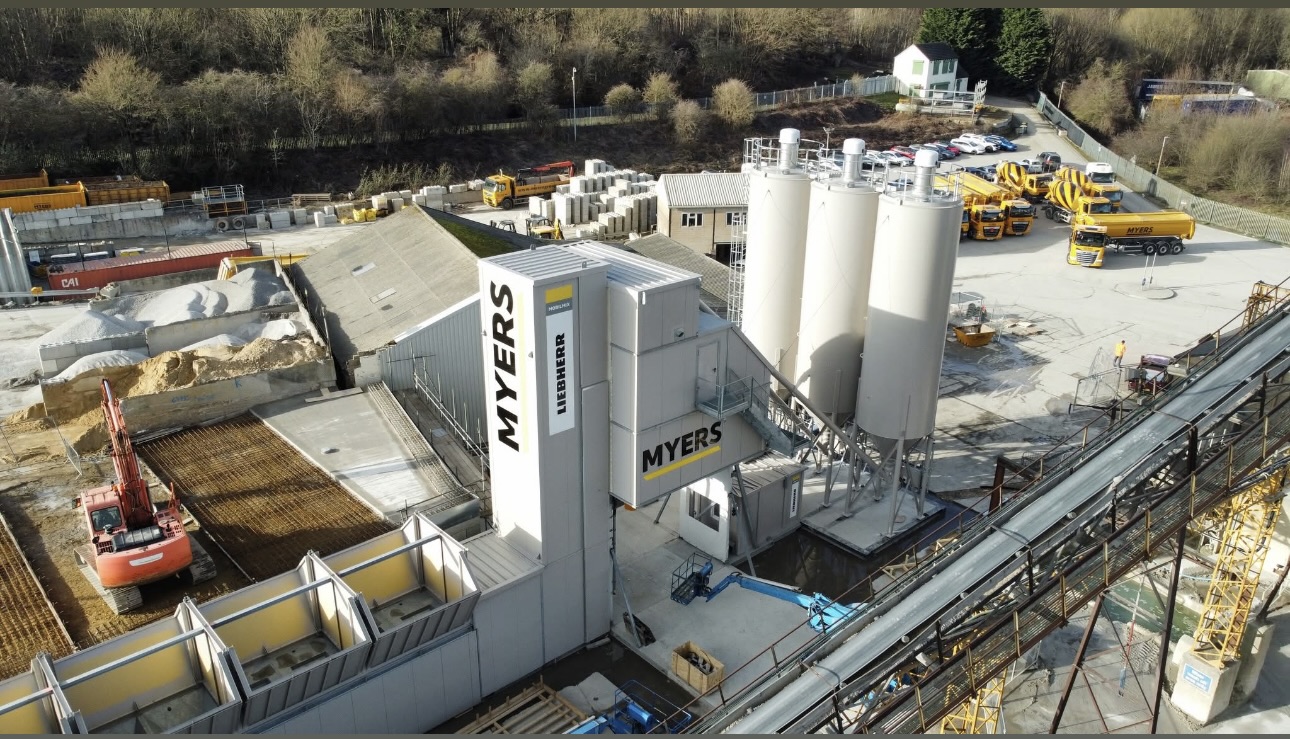
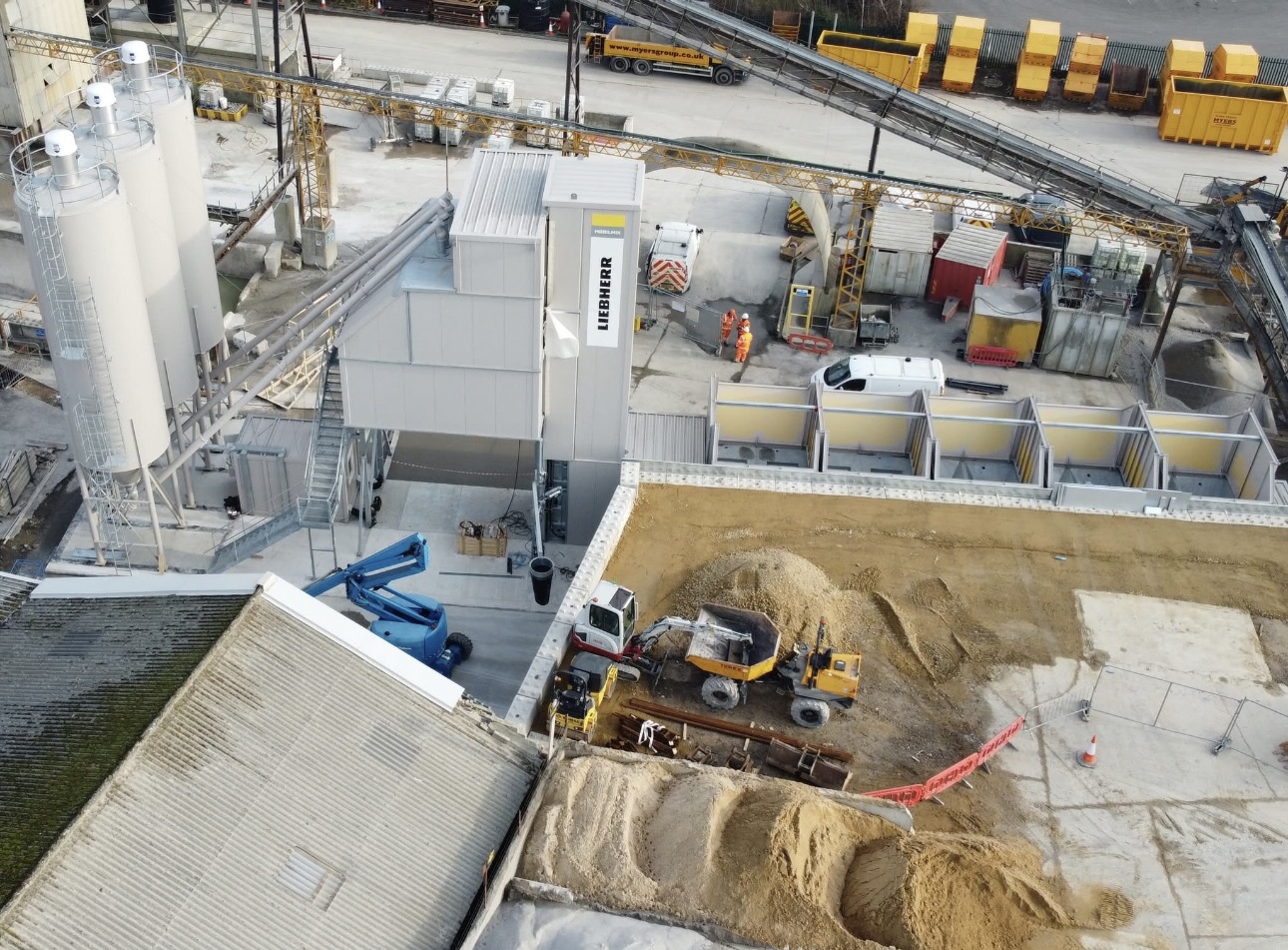

Our Safety Scope and Contributions
Our scope as Principal Designer included:
- Leading safety led design reviews and working with the design team to identify and eliminate foreseeable risks
- Providing planning and support for RAMS and other required documentation under CDM 2015
- Giving design input into equipment access, fall protection, and guarding across the site layout
- Ensuring lock-out/tag-out procedures were planned into the equipment installation and maintenance plans
- Making sure CDM regulations were followed and that all parties understood their legal duties
The result was a facility that is not only highly productive but also designed with:
- Operator safety in day to day use
- Ease of inspection and maintenance built into the design
- Zero harm principles throughout the working environment
- Full compliance with CDM Regulations 2015
Collaborating with Industry Leaders
This project brought together two highly respected names in construction:
- Liebherr brought world class batching technology, with proven reliability and advanced engineering
- Myers ReadyMix provided operational expertise and a clear vision for long term site performance
- We brought practical planning, strong communication, and hands on coordination to make it happen, safely and on time
Project Outcome
This concrete batching plant in Huddersfield was delivered:
- On time
- On budget
- With zero incidents
- With long term operational safety designed in from day one
It now serves as a critical supply hub for infrastructure, commercial and housing projects across West Yorkshire, and a benchmark example of what good looks like when health and safety is built into the project, not bolted on later.
Need a Principle Designer For Your Next Project?
We’ve helped businesses like Myers deliver complex, high risk builds safely and on time. If you’re planning something similar, let’s talk about how we can help.
Want to Learn More About Our Previous Projects?
Check out more of our health, safety, and environmental work across construction and manufacturing.
Looking for ongoing Safety Support?
We act as your competent person and handle all your health, safety and environmental responsibilities, so you don’t have to.